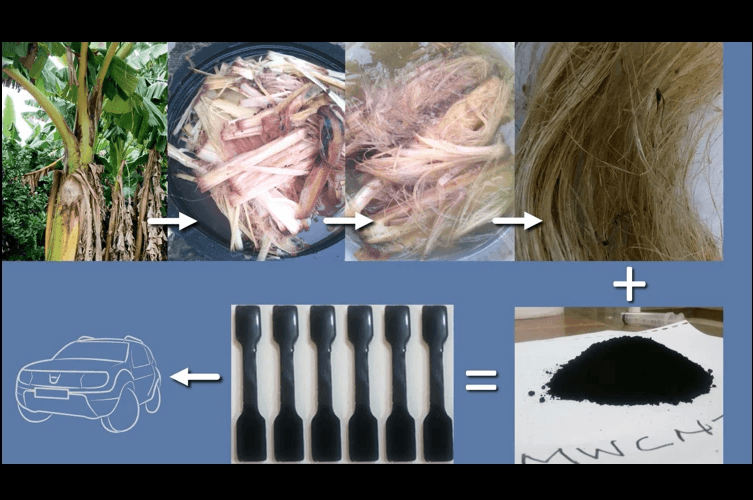
Image credit: EurekAlert
Researchers from the University of Johannesburg have come up with a solution to make vehicles lighter with plantain fibre. With lighter vehicles, their fuel efficiency can also be increased.
About â…“ of a vehicle is made of plastic. Most of these hard plastics are resistant to biodegrade and responsible for a large part in the plastic pollution. But in recent years more and more automotive companies are trying to replace their plastic auto parts into more environment-friendly solutions. The use of natural fibres like Flax panels, Hemp or Wood for panels, engines and for noise cancellation are such applications. Although these greener options are easy to biodegrade they can be easily crack, break or bend upon impact. This is where the Plantain (Musa paradisiaca) comes in. They are said to be easily moulded, durable and do not corrode while being light on the environment.
Although there are other carbon-based options for stronger and lightweight auto parts, they do come with an expensive price tag. Replacing them with natural Plantain fibres is more cheaper and sustainable at the same time. These plantain fibres come from agricultural waste. The part of the plant used here is called the pseudo-stem which is inedible.
To treat the Plantain pseudo-stems, first, they undergo a process called the ‘water-retting’ where the individual fibres get separated. Then they are immersed in a 3% caustic soda solution for 4 hours. The dried plantain fibres are then treated with high-frequency microwave before combining with multiwalled carbon nanotubes (MWCNT) using a single epoxy resin. The best combination of plantain fibres to resin/ nanotubes is 1 to 4. The carbon nanotubes’ contribution is only 1% in the end product.
The hybrid nature of this composite has resulted in ‘substantial impact on the mechanical properties of the hybrid composites as mechanical strength were enhanced to about 50%. Hardness and Impact strength showed an improvement of up to 20% and 27% respectively as carbon nanotube content increases from 0.5% to 1% wt. Thermal conductivity has shown significant improvement by up to 43%’. In hardness, they were far stronger and stiffer than resin only material.
With few more tweaks in the process, the researchers hope this material would be ready for the automotive manufacturing industry. This will bring lighter vehicles which results in fuel efficiency and safety.